Our approach to inventory planning focuses on managing the supply chain for inherent variability and risks while engaging in continuous improvement activities to reduce such uncertainties. Caledonia develops a tailored solution based on the client’s distinctive business environment, industry standards, operational challenges, and financial goals.
Initial assessment
We start by understanding the expectations of the key supply chain elements—customers, internal operations, and suppliers. We follow this with a detailed review of the company’s current inventory model and an analysis of volatility across the supply chain. This involves (1) extracting data from ERP systems and (2) analyzing large quantities of transactional data at an SKU level from the past several years. These two steps help us establish the key drivers of current inventory levels and delivery performance, and the effectiveness of the current system in meeting customer requirements. We follow this with sensitivity analysis to understand the impact of changes to the key inventory drivers (such as lead times, order quantities, batch sizes, and customer service goals) on inventory costs and working capital. This assists us in developing directional estimates on what optimal inventory levels should be.
Comprehensive inventory plan
The focus of the next phase is an inventory model that minimizes inventory while maintaining customer service levels, lead times, and operational costs of the entire value stream. Our modeling principles, simulation techniques, and planning methodology are at the leading edge of “lean” thinking, and espouse the principles of “Factory Physics” made popular by prominent academics from the University of Michigan and Georgia Tech. We develop a Plan for Every Part (PFEP) that accounts for variability in demand and lead time and establishes the optimal inventory level at an SKU level. We analyze the distribution network and optimize hub and spoke systems for maximum efficiency in cost and working capital. We work with the client’s suppliers to move towards just-in- time deliveries. The most critical piece of our work is integrating our inventory models with the client’s financials to develop a holistic picture of the impact of the new system.
Optimizing production batch size for better inventory turns. Most production systems are constrained by the time it takes to set up the production equipment, resulting in long production runs and large batch sizes of a given part. While companies work to lower set-up time, the limited availability of capacity should be properly utilized for higher inventory turns, while keeping set-up costs low. This is particularly challenging when involving a large number of SKUs and equipment with complex value streams. Caledonia can extract production standards and actual production history from the client’s ERP system and use Monte Carlo simulation techniques to identify optimal batch- size requirements.
Implementation
The scope of a Caledonia engagement extends beyond developing recommendations and models for our clients. We work hands-on with cross-functional client teams that involve materials, suppliers, operations, finance, and IT to develop, train, and implement the required systems and tools for the new inventory system. Some common tools we will develop will be used in managing capacity, calculating inventory requirements, optimizing batch size, managing open customer and vendor orders, and designing dispatch reports to manage production. Visual systems are developed to ensure the simplicity of the system for the end users. Metrics are setup to track and drive continuous improvement activities at every level.
Illustrations of variability driven inventory planning
The following chart explains a typical distribution of the variability in demand between the top 80% of SKUs (A), the next 15% (B) of SKUs, and the bottom 5% (C). Also, the 80-20 rule applies to the number of SKUs under A, B and C, i.e. 20% of the SKUs makes up 80% of the revenue.
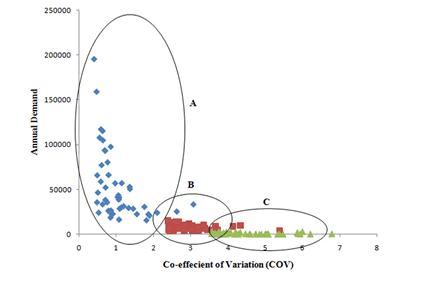
Most companies typically design a generic inventory policy that applies to all SKUs and this policy is usually arrived at through trial and error and years of experience. The evolution of such a blanket policy across all SKUs will focus on meeting the delivery requirements of the most sporadic items, i.e. the low volume, highly variable items (C items). Essentially, the materials management system is designed around the bottom 5% of the company’s business. The unintended consequence of this one-policy system is that it results in excess inventory on the high volume, low variable A items, which are basically 80% of the inventory. Higher excess and obsolete (E&O) inventory on lower volume items is another consequence that drives up costs. Caledonia, by analyzing variability and seasonality at an SKU level, will leverage the lower variability of higher volume items to reduce the client’s working capital while maintaining similar or better delivery performance.
The charts below demonstrate the impact of variability on inventory requirements. The three items below have identical average demand (~180), vendor lead-times (70 days), and delivery requirements (95%), but have a big difference in the demand variability. Demand for Item X is more stable than Item Y (see next graphic), and Item Y more stable than Item Z (see following graphic). Most trial-and-error systems will assign a higher safety stock for all three items based on their averages in order to be able to take care of the highest variable item (8,233 for all three items). In contrast, Caledonia’s approach would result in lower inventory requirements for the first two items. Thus, less capital would be invested in inventory.
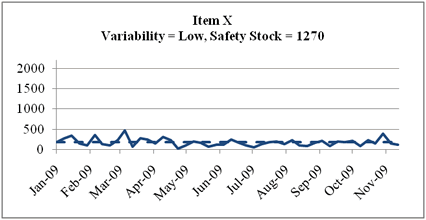
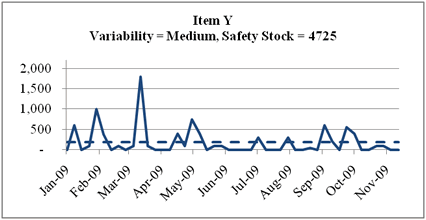
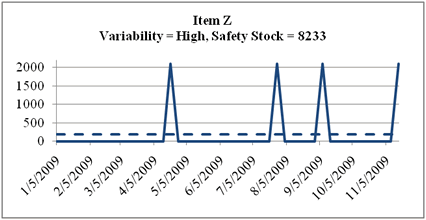
|