By J.W. Henry Watson, principal, and Charles Standard, senior
consultant, Caledonia Group Inc.
In early
November, the Federal Reserve lowered the discount rate for the third time
since September 11 and the tenth time since the economy began slowing more
than a year ago. Because the first nine rate cuts failed to stem the
economy's slide, can even Alan Greenspan be betting that the latest move,
which puts the rate at its lowest point in 40 years, will do the trick?
Indeed, more than most economic downturns, this one is
likely to end as the result of thousands of companies turning around their
operations. What will be the basis of successful turnarounds in
manufacturing? To paraphrase an old adage, perhaps "what's good for Ford
is good for the country."
Under the new leadership of William Ford and the top
people he's chosen, the automaker has increased its commitment to
implementing the Ford Production System. This is Ford's version of the
Toyota Production System, which over the last decade has become known
generally as lean manufacturing or lean production.
That Toyota has continued to thrive during the current
economic slowdown, racking up higher profits and market share, is a fact
that Ford and legions of other companies are unlikely to overlook. In
addition, General Motors, which has had greater success in implementing
lean thinking, has pulled decisively ahead of Ford in quality and
productivity.
Lean manufacturing seeks to minimize unnecessary time,
materials and effort throughout the entire value chain, from raw materials
to the ultimate customer. It is both a new way of thinking about
production and a distinct system of production in its own right. When
implemented properly, it can produce astonishing results.
Typically, lean manufacturing reduces inventory by 30 to
50 percent, lead times by 40 to 75 percent and floor space requirements by
30 to 50 percent. At the same time, quality improves by 25 to 50 percent,
and productivity increases 30 to 50 percent.
Systematic Implementation
Lean manufacturing is often characterized inaccurately as simply a
collection of best practices, and countless books and articles explain how
to use commonly known lean techniques. This has expanded the general
awareness, practices and potential benefits of lean manufacturing, but it
has also led to piecemeal application of its tools and techniques, which
generally provides little or no lasting benefit.
Lean manufacturing is not a new concept. Ford has been
trying with various degrees of commitment to implement lean thinking for
about 20 years. That the company has not yet succeeded suggests that while
the direction is obvious, the path is less so.
A key to finding a successful path is the systematic
implementation of all aspects of a lean production system. This requires a
commitment from top management down to personnel on the plant floor.
However, a commitment by top management and the systematic implementation
of all pertinent lean practices are often lacking, especially in
turnaround situations. It is easy to slip into a "firefighting" mode,
which simply does not create sustainable improvement.
Many companies leave out critical elements of lean
thinking. The most glaring omission is often lean materials management,
which includes implementing pull systems, both internally and externally.
External pull systems should involve both suppliers and customers, and
schedules need to be stabilized.
A study by R.R. Fullerton and C.S. McWatters that
appeared earlier this year in the Journal of Operations Management (Vol. 19) attempted to determine which aspects of lean manufacturing were
responsible for business performance improvement at 447 U.S.
manufacturers. By analyzing the practices and performance of these
companies, the study found that two unique lean practices--just-in-time
(JIT) purchasing and pull system implementation--were significantly
related to 10 of the 15 performance measures used in the study. Both are
key to material flow and production planning.
But corporate renewal professionals might counter that
the typical company they see does not have bills of material worthy of the
name. The company contends that the bills will be fixed "soon," but soon
never arrives.
The companies that turnaround professionals are called on
to help often take physical inventories daily because they don't know what
they've made, shipped or scrapped. They think progress on inventory
accuracy is getting to 80 percent, day over day. A whole team is devoted
to expediting incoming materials to address unanticipated stockouts.
In addition, turnaround professionals often find that
material and capacity planning are unreliable because everything changes
by mid-morning to deal with screaming customers whose production processes
are being shut down by quality spills and late deliveries. Equipment
maintenance stopped months ago and uptime charts look like this year's
Nasdaq index. Then there are the product launches that someone must have
thought would happen magically.
Lean material systems are not only better for supporting
world-class companies, but they also yield major benefits rapidly when
deployed properly in out-of-control situations--and they do not require
huge capital expenditures or massive information systems implementation
efforts.
Fundamental Changes
Lean material systems can generally be implemented in phases. Major
improvements are soon evident, and the systems change the fundamental way
a business works for the better. But where does one start?
As a first step, schedules must be stabilized. One of the
primary material management principles of lean thinking is to level
schedules. Last-minute schedule changes must be prohibited, and major
moves among plants or from one production line to another should not be
allowed.
Materials must flow smoothly from the supplier to the
customer. Material handling should be eliminated as much as possible
throughout the operation. Schedules should meet shipping plans rather than
support large batches, and they should reflect proven capacity, not some
illusion of capabilities. Speed of material flow is very important in such
a system, and preparing a value stream map is extremely useful in
implementing these changes.
At the same time, data must be accurate. This usually
means eliminating backflushing, the practice of relieving inventory
through bills of material based on finished goods production. Backflushing
is often at the root of inventory accuracy problems.
Tracking of work-in-process (WIP) inventory on corporate
information systems should be eliminated. In its place a system that uses
pull signals to replenish raw materials should be instituted. This should
be done in the context of simple blanket purchase orders, and the practice
of triple-matching purchase orders, receivers and invoices should be
eliminated. Payment should be triggered by receipt of the receiver.
Problem solving teams comprised of people from the floor
who actually make the transactions should be established. Every possible
step in their usual activities should be eliminated to streamline
processes, and the root causes of repeated mistakes should be identified
and eliminated.
This floor-based effort usually uncovers numerous setup
errors in the information system. The idea that transactions are cheap
because they are computer-based must be banished. The probability of
success declines exponentially as transaction volume rises--high
transaction volumes create an impenetrable information fog.
A company should move aggressively to relieve inventory
directly, based on pull system signals, or it should issue materials from
controlled stock-keeping locations. Typically this effort reduces the
number of transactions on the information system by more than an order of
magnitude--by more than 90 percent. Stockouts will be eliminated as
discipline is imposed on a much simpler system.
Doing all of this does not create a simpler system; it
creates a fundamentally different system. Traditional material resource
planning (MRP), or push materials systems, manage production based on
forecasts of production capability and demand, as well as on orders.
Production is initiated by the forecast or order and is independent of the
situation in the plant. As a result, inventory--and especially WIP--can
fluctuate wildly as both production throughput and demand deviate from
planned levels.
WIP and finished goods inventories build up in specific
areas as a result of forecast errors and production bottlenecks. At the
same time, there are spot shortages of WIP in many operations and missed
customer deliveries. Equipment is alternatively over loaded and starved,
driving costs through the roof.
This is how that all-too-common paradox of inventory
bloat accompanied by production problems and declining shipments comes
about. This bleak scenario happens whenever there is variability in
demand, productive capability or lead time. If one does not get you,
another will. Any system that builds to forecast rather than to demand is
a system that will fail.
Controlling Inventory
Pull systems are designed to hold raw material, WIP and finished goods
inventory stable by adjusting throughput. If the next machine in a process
is broken, production should be stopped when a predetermined level of WIP
is reached. Reserve capacity should be maintained to support recoveries
and to deal with unanticipated downtime or temporary demand increases.
WIP levels should be set to protect against disruptions
that occur in manufacturing plants. Some maintain that inventory should be
lowered so that weaknesses in the system can be exposed more easily. But
with a passel of furious customers screaming at the door, this approach
has limited appeal.
Instead, the flow through the system should be
stabilized, the weaknesses identified and eliminated, and then inventory
should be lowered. But there is a paradox in this. Inventory falls, often
dramatically, as a result of implementing lean materials management,
despite the provision of significant inventory to protect against process
interruptions. This results from controlling inventory rather than
allowing it to be determined by an unstable system.
Because of the stabilizing effects on production flow and
other benefits, pull production control is an integral part of an overall
lean manufacturing system. It may seem reasonable, therefore, to expect
pull systems to be used frequently and implemented early in a lean
manufacturing transformation or turnaround situations. However, empirical
evidence does not support this.
Pull systems are often among the last lean practices
implemented. The authors have encountered more resistance to pull
implementations than to any other aspect of lean turnaround efforts.
Furthermore, even after pull systems are implemented and create major
benefits, most management teams stubbornly attribute the gains to other
causes.
A study by B.B. Flynn, S. Sakakibara and R.G. Schroeder,
which was published in the Academy of Management Journal (Vol. 38,
No. 5, 1995), found that pull systems were the least frequently used of 12
essential lean practices. A 1997 study conducted by J.A. Brox and C. Fader
and published in the Journal of Operations Management (Vol. 15)
found that pull systems were used only occasionally, ranking number 14 out
of 17 selected lean practices.
A 1999 study by RE. White, J.N. Pearson and J.R. Wilson,
which was published in Management Science (Vol. 45, No. 1), found
that pull system implementation ranked number eight out of 10 common lean
practices. A 2000 study by J.L. Callen, C. Fader and I. Krinsky, which was
published in the International Journal of Production Economics (Vol. 63), found that pull systems were used less than half the time, even
among companies that claimed to have implemented lean practices on a
global basis.
Resistance to Pull Systems
Perhaps one reason manufacturing managers are reluctant to implement
pull systems is that they lack a good conceptual understanding of what
such a system is. Fundamentally, a pull system is a consumption-based
replenishment system.
Consider an automatic icemaker, which operates as a pull
system. In its steady state, the icemaker has a finite buffer of ice cubes
waiting in a tray. Eventually, as ice cubes are consumed, the quantity in
the buffer falls below a threshold, a mechanical sensing arm detects this
change and more ice cubes are produced to replenish the buffer.
An icemaker that operated on a push principle would work
from a forecast that predicted when and how many ice cubes would be
consumed throughout the day. The icemaker would then be set up to produce
ice cubes according to this schedule. In theory this should work well, but
in practice, the system would be inherently inflexible. If ice cube
consumption deviated from the predicted pattern for any reason--dinner
guests or cold weather, for example--the push system might experience a
stockout or an overabundance of ice cubes.
This occurs with some types of enterprise resource
planning (ERP) systems in manufacturing companies. The push approach to
production control allows stockouts of critical items and production
overruns of other items, which disrupt workflows and cause congestion in
the factory. Often, highly capable materials managers and production
supervisors are forced to develop off-line (pull-type) procedures to work
around these dysfunctional systems.
Recently, executives at two of America's largest private
equity funds said that failed ERP implementation is the primary reason for
poor performance in their portfolio manufacturing companies. Such systems
can support pull scheduling and can be major value enhancers when they do
so. How to achieve this is beyond the scope of this article.
Another reason for the lack of pull system implementation
is that it requires managers to conceive of their operations in a totally
new way. The profitability of the overall operation must take precedence
over the profitability of individual departments or processes.
For example, if a downstream process produced parts more
slowly than normal, perhaps due to a maintenance problem, it would not
consume components at the anticipated rate. This means that replenishment
signals would arrive at an upstream process less frequently than expected.
Fewer replenishment signals would lower production output requirements at
the upstream process. This, in turn, would mean less absorbed overhead for
the upstream department, and temporary layoffs or underutilized hourly
labor would result.
If the upstream process were operating under a push
system, it would continue to produce parts at the normal rate, without
regard for disruptions in the downstream operation. This would allow the
upstream department to achieve its production and financial targets at the
expense of increased congestion, excessive accumulation of WIP and longer
cycle times. These factors increase production costs.
Adopting pull production control requires managers to
look beyond the efficiency of a single process or department and make
decisions that are more profitable for the operation as a whole.
Another important reason for the resistance to
implementing pull systems in the American manufacturing community is that
there is widespread conflicting information about when, how, and even if
such systems should be implemented. For example, some researchers provide
a litany of requisite improvements that must be in place before a pull
system can be attempted: elimination of waste, improved process design,
standardized operations, level production schedules, short setup times,
short lead times, a smooth production schedule, small-lot production, low
inventory, excellent quality, and a host of others.
These "prerequisites" are excellent general
recommendations for operations improvement, and many offer significant
benefits in their own right. Nevertheless, there is nothing about any of
these improvements that uniquely prepares a factory for pull system
implementation. Those who insist on these as precursors to such a system
are discouraging manufacturing managers from pursuing pull systems at all.
One benefit from implementing a well-designed pull system
is the sharp reduction in stockouts. Without stockouts, production flows
are much smoother, and inventory and lead times can be reduced
accordingly. These instantaneous benefits of pull system implementation
are realized regardless of other operational issues that would otherwise
hinder performance.
One of the greatest strengths of pull production control
is its robustness and insensitivity to implementation errors and
unsatisfied assumptions. Pull systems work well in the presence of
variability and uncertainty, and they provide many of the same benefits
that are associated with other more general operational improvements.
Implementing pull production control can help a manufacturer to realize
those benefits while other improvements are pursued at the same time.
Summary
There is nearly universal recognition that lean thinking is a
requirement for long-term competitive survival in manufacturing. Indeed,
for many companies, skill at lean manufacturing is becoming the one
enduring and sustainable competitive advantage. As a result, any
operational turnaround plan that does not make systematic implementation
of lean manufacturing a core element is unlikely to succeed in creating
stakeholder value.
A successful turnaround begins with a plan for systematic
implementation of lean manufacturing across all aspects of operations. The
turnaround plan must put immediate emphasis on lean materials flow,
including such factors as pull systems, leveling of schedules, and
accurate control of inventory, including WIP. A company that follows this
plan will see immediate operating improvements.
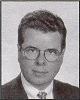 |
J.W. Henry (Harry) Watson is the managing principal of
Caledonia Group Inc., a Detroit-based management consulting firm
that specializes in lean assessments, implementing lean systems, and
operating turnarounds. |
 |
Charles Standard is a senior consultant at Caledonia Group
and the author of Running Today's Factory: A Proven Strategy for
Lean Manufacturing, which won the Shingo Foundation Prize for
excellence in manufacturing research in 2000. |
|