By J.W. Henry Watson, Principal, Caledonia Group
Inc.
Out of fashion
for half a century, scientific management is becoming respectable again.
Probably because scientific methods are at the heart of the Toyota
Production System, a system credited with keeping Toyota the world
standard for excellence in manufacturing and service since the early
1970s.
The scientific method also underpins Toyota-like systems
known as "synchronous" or "competitive" manufacturing and activity-based
management. In a 1990 book, three MIT scholars re-named the Toyota
Production System "lean" production. Today, lean production and lean
thinking are the names associated with a particular set of tools and
practices, as well as a business operating system and philosophy
(pioneered and refined by Toyota over 50 years) that have revolutionized
automobile manufacturing worldwide. Lean production moved beyond the
automotive industry during the 1990s, and in recent years has moved beyond
manufacturing.
There are several reasons why this is of interest to the
turnaround industry. One, an increasing number of troubled companies need
more than financial management and restructuring. They need to improve
operations because their real problems stem from the fact they lag their
competitors in reaching world-class benchmarks for efficiency, quality,
delivery and cost. Two, in a typical, non-lean operation, lean has a track
record of reducing inventory by 30 to 50 percent, reducing lead times by
40 to 75 percent, improving quality by 25 to 50 percent and improving
productivity by 30 to 50 percent. Moving to lean is the cheapest and
quickest way to achieve a turnaround in operations. And, three, because
lean improvements begin immediately and typically reduce capital
expenditures and working capital needs (compared to what they otherwise
would have been), the initial cost of implementing lean usually pays for
itself through reductions in working capital and operating costs.
There is a caveat, however. While implementing a lean
system can be relatively cheap and quick (depending on the type and size
of operation, 18- to 24-months with major progress achieved in the first
six months), change is always a challenge. Owners and senior management
need to develop an appreciation of lean and must be committed to
transforming the company. Introducing some pieces of a lean system in
isolation won't produce sustainable results.
Perspectives on Lean Production
This article reviews two recent publications that
contain, from different perspec tives, a wealth of information about lean
production and lean thinking.
The first is an article, "Decoding the DNA of the Toyota
Production System," by Steven Spear and H. Kent Bower, two Harvard
Business School professors. The article appears in the September-October
1999 issue of the Harvard Business Review. This article provides a
good introductory summary (10 pages) of what a lean system is and how it
works. The second is a book, Manufacturing Ideology: Scientific
Management in Twentieth-Century Japan, by University of Kansas history
professor William M. Tsutsui. In the process of developing an
unconventional, but interesting, thesis on the genesis of Japanese-style
management, Tsutsui provides a rich history of the decades long evolution
of the Toyota Production System, including telling glimpses of the
single-minded commitment of Toyota's leaders to scientific management.
The Spear and Bowen article is based on an extensive
four-year study they undertook of the inner workings of some 40 companies
in the U.S., Europe and Japan, some using the Toyota Production System,
some not. The companies studied include both process and discrete
manufacturers whose products range from prefabricated housing, auto parts,
cell phones and computer printers to injection-molded plastics and
aluminum extrusions. The authors stress that the key to understanding the
Toyota Production System is recognizing that "whenever Toyota defines a
specification, it is establishing sets of hypotheses that can then be
tested. In other words, it is following the scientific method."
Spear and Bowen capture in four basic rules the tacit
body of knowledge that underlies lean production. The first rule governs
the way workers do their work, the second governs the way they interact
with one another, the third governs how production lines are constructed
and the fourth addresses how people learn to improve.
Rule 1. All work shall be highly specified as to content, sequence,
timing and outcome.
Requiring that every activity be specified seems simple
enough. The authors claim, however, that in reality most managers don't
take this approach to work design and execution, even when they think they
do. The problem is that most specifications allow, and even assume, some
variation. Before long, there is plenty of scope for a new employee to do
the job a little differently than specified, which translates into poorer
quality, lower productivity and higher costs. When Rule 1 is rigidly
adhered to, workers follow a well-defined sequence of steps when doing a
particular job, with the result that it is instantly clear when they
deviate. Even complex and infrequent activities, such as training an
inexperienced workforce at a new plant, launching a new model, changing
over a production line or shifting equipment from one area of a plant to
another, are designed according to the rule.
At one plant the authors visited, equipment from one area
of the plant was moved to create a new production line in response to
changes in demand for certain products. Moving the machinery was broken
into 14 separate activities. Each activity was then subdivided and
designed as a series of tasks. A specific person was assigned to do each
task in a specified sequence. As each of the machines was moved, the way
the tasks were actually done was compared with what was expected according
to the original design, and discrepancies were immediately signaled.
In demanding that people do their work as a highly
specified sequence of steps, Rule 1 forces them to test hypotheses through
action. Performing the activity tests the two hypotheses implicit in its
design. First, that the person doing the activity is capable of performing
it correctly and, second, that performing the activity actually creates
the expected outcome. If the activity isn't done in the specified way in
the specified time then at least one of these hypotheses is refuted,
thereby indicating that the activity needs to be redesigned or the worker
needs more training.
Rule 2. Every customer-supplier connection must be direct, and there
must be an unambiguous yes-or-no way to send requests and receive
responses.
Another way of saying this is that every connection must
be standardized and direct, unambiguously specifying the people involved,
the form and quantity of goods and services to be provided, the way
requests are made by each customer and the expected time in which the
requests will be met. This creates a supplier-customer relationship
between each person and the individual who is responsible for providing
that person with each specific good or service. When a person needs a
part, for example, there is no confusion over who will provide it, how the
request will be triggered (usually with a kanban card), or what part will
be delivered.
Many companies devote substantial resources to
coordinating people, but in most plants requests for materials or
assistance often take a convoluted route from the line worker to the
supplier via an intermediary. Any supervisor can answer any call for help
because a specific person has not been assigned. The drawback, as all lean
experts recognize, is that when something is everyone's problem it becomes
no one's problem.
Under Rule 2, a worker encountering a problem is required
to ask for assistance at once and must receive help from the specified
person within the worker's cycle time, which could be only 55 seconds. If
the prob lem is not resolved within the specified time, the hypothesis in
the customer-supplier connection for assistance is immediately challenged.
The authors note that this requirement is difficult for managers
accustomed to encouraging workers to try to resolve problems on their own
before seeking help. But if this happens, problems remain hidden and are
neither shared nor resolved company-wide. If workers begin to solve
problems themselves and arbitrarily decide which ones to seek help for,
problems mount and valuable information about the real causes of the
problem may be lost.
Rule 3. The pathway for every product and service must be simple and
direct.
When production lines are designed in accordance with
Rule 3, goods and services do not flow to the next available person or
machine but to a specific person or machine. If for some reason that
person or machine is not available, Toyota will see it as a problem and
might require that the line be redesigned. The stipulation that every
product flow in a simple, pre-specified path doesn't mean that each path
is dedicated to only one particular product, however. Each production line
adhering to lean principles typically accommodates many more types of
products than its counterpart in a non-lean company.
This rule not only applies to products but to service
requests as well. When a worker needs help and if the specified supplier
of that help can't provide it, he or she, in turn, has a designated
helper. In some lean plants, this pathway for assistance can be several
links long, connecting the factory floor worker to the plant manager. By
requiring that every pathway be specified, the rule ensures that an
experiment will occur each time the path is used.
Rule 4. Any improvement must be made in accordance with the scientific
method, under the guidance of a teacher, at the lowest possible level in
the organization.
For people to consistently make effective change, they
must know how to change and who is responsible for making the changes.
Lean production explicitly teaches people how to improve. This rule states
the process for making any improvement to production activities, to
connections between workers or machines or to pathways. But how do people
learn the scientific method? Learn to improve? Spear and Bowen illustrate
this by relating their visit to a mattress company. Since 1986 the
different types of mattresses produced at this company has grown from 200
to 850, its volume has grown from 160 mattresses a day to 550 and its
productivity has doubled.
The authors studied a team of mattress assembly workers
who were being taught to improve their problem-solving skills by
redesigning their own work. Initially, the workers had been responsible
for doing only their own standardized work; they had not been responsible
for solving problems. Then the workers were assigned a leader who trained
them to frame problems better and to formulate and test hypotheses. The
results were impressive. The team's redesign of the way edging tape is
attached to the mattresses reduced the defect rate by 90 percent.
To make changes, people are expected to present the
explicit logic of the hypotheses. The improvement effort must also be
designed as an experiment with an explicit, clearly articulated,
verifiable hypothesis such as: If we make the following specific changes,
we expect to achieve this specific outcome. Further, they are expected to
question their assumption deeply enough to fully exploit all the
improvement opportunities available to them. Teams are taught that how
they make changes is as important as what changes they make.
Who does the improvement? Frontline workers make the
improvements to their own jobs, and their supervisors provide direction
and assistance as teachers. If something is wrong with the way a worker
connects with a particular supplier within the immediate assembly area,
the two of them make improvements, with the assistance of their common
supervisor. When changes are made on a large scale, improvement teams are
created consisting of the person directly affected and the person
responsible for supervising the pathways involved.
All the rules require that activities, connections and
flow paths have built-in tests to signal problems automatically. It is the
continual response to problems that makes this seemingly rigid system so
flexible and adaptable to changing circumstances.
How Do Workers Learn the Rules?
Managers in lean enterprises don't tell workers and
supervisors specifically how to do their work. Rather, they use a teaching
and learning approach that allows workers to discover the rules as a
conseqnence of solving problems. For example, the supervisor teaching a
workshop group or individual the principles of the Rule 1 will go to the
work site and observe while asking a series of questions. How do you do
this work? How do you know you are doing this work correctly? How do you
know that the outcome is free of defects? What do you do if you have a
problem?
This continuing process gives the group or person
increasingly deeper insights into the work being done. From many
experiences of this sort, workers gradually learn to generalize how to
design all activities according to the principles embodied in Rule 1. All
the rules are taught in similar Socratic fashion of iterative questioning
and problem solving.
Not surprisingly, Spear and Bowen display a little
arrogance in spots and also a bit of ignorance here and there. They claim,
for example, that the Toyota Production System "grew naturally out of the
workings of the company over the past five decades and as a result has
never been written down." Moreover, they claim that "Toyota workers often
are not able to articulate it." They also state that few enterprises have
managed to imitate Toyota successfully because the Toyota Production
System is a paradox. (On the one hand, every activity, connection and
production flow is rigidly scripted. Yet at the same time, Toyota's
operations are enormously flexible and responsive to customer demand.) The
paradox disappears, they claim, when the system is properly viewed as a
continuous series of controlled experiments.
In fact, there are whole libraries on the Toyota
Production System and books galore on other Toyota-like systems. While the
article does a good job of summarizing, the same ideas are in the books.
About the only thing missing in other work is the focus on scientific
management, mainly because it has been controversial, though accurate.
Also, lean production (which, recall, is the name a couple of MIT
professors gave to the Toyota Production System) has been successfully
implemented in scores of companies that I have personal, direct knowledge
of. Lean production principles and tools have even been used with great
success to achieve dramatic improvements in medical procedures such as
open-heart surgery. The "paradox" the authors speak of is taught in
industrial engineering courses in schools such as the University of
Michigan and MIT--but not as a paradox.
Before getting into the Tsutsui book, a brief word about
Frederick Winslow Taylor, the father of scientific management (it's on his
tombstone). "One-best-way" Taylor was the world's first management
consultant and efficiency expert. His life (he lived from 1856 to 1915)
coincided with the Industrial Revolution at its height and he is credited
with speeding up the fruits of that revolution more than any person before
or since. Management guru Peter Drucker calls Taylor's ideas the most
powerful as well as the most lasting contribution America has made to
Western thought since the Federalist Papers.
Drucker is referring primarily to Taylor's "time and
motion" studies, his work in standardizing tools, parts and shop floor
methods and related efforts aimed at gaining production efficiencies. Even
his enemies grant that Taylor's work exponentially boosted productivity
and quality--and living standards.
But Taylor, a wealthy aristocrat, had his weaknesses. He
definitely didn't favor (probably gave little thought to) the kind of
employee involvement required for a lean production system to succeed. He
tended to segment workers into "brain" and "brawn" groups. His detractors,
then and now, accuse him of overworking and enslaving employees, reducing
skilled mechanics to common laborers and denying workers a voice. Labor
rebelled and trashing scientific management began.
Tsutsui's thesis is that so-called Japanese-style
management, widely admired in the West since the 1970s and touted as
uniquely Japanese, is little more than Taylorism, "revised" to include
quality control circles and worker involvement. (Note: Toyota is the
poster child of Japanese-style management; Honda and Nissan, for example,
like most of their Western counterparts, have been less successful in
implementing lean.) To build his case, Tsutsui painstakingly scrutinizes
(decade after decade) the actions and statements of the Toyota Production
System's primary architects (Toyota founder Toyoda Kiichiro, Ono Taiichi
and Shingo Shigeo) for ways to connect these "Taylorism" and "Taylorite"
ideas. Fortunately he finds plenty and for the reader interested in
scientific management and the evolution of the Toyota Production System,
the result is a pretty thorough education in both.
In 1937, for example, Kiichiro established the "flow
production system" and the just-in-time concept at Toyota's first
automobile plant. This required explicit work standards and strict labor
regimes. Tsutsui's comment: "Another Taylorite preoccupation reaffirmed in
the Toyota system." Taiichi, he says, "sought to eliminate all unnecessary
movements and allow no idle time, for machines or workers. Another quote
from Taiichi: "Unless all sources of waste are detected and crushed,
success will always be just a dream." And again: Taiichi's "conspicuous
success in boosting labor productivity was due to time-and-motion study
and layout design, the two Tayorite methodologies most highly developed in
Japan." He quotes Shigeo, avowing at that the end of his career: "My
thinking is based on Frederick Taylor's analytical philosophy."
My favorite: Despite postwar conditions in Japan's
political economy that would have permitted change [from scientific
methods], "the logic of Taylorite solutions--most basically, the drive to
wring the utmost efficiency out of existing facilities and personnel
through incremental change--remained firmly engrained in the consciousness
of Japanese managers."
What's most interesting is that Spear and Bowen treat
scientific methods as positive and uncontroversial. Tsutsui, on the other
hand, adopts a hostile tone toward "Taylorism," but in producing a
scholarly work has, probably unwittingly, presented a positive case for
scientific management.
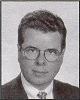 |
Harry Watson is founding principal of Detroit-based Caledonia
Group Inc., which specializes in lean assessments and
implementations. |
|